In today’s fast-paced warehousing and logistics industry, companies continually seek ways to improve efficiency, reduce costs, and enhance worker safety. One of the most effective ways to achieve these goals is by implementing ergonomic palletizing equipment. Traditional palletizing methods often involve repetitive bending, lifting, and twisting motions, which can lead to musculoskeletal disorders (MSDs), fatigue, and workplace injuries. By integrating ergonomic solutions, businesses can improve productivity while prioritizing employee well-being.
Why It’s Important
Palletizing is crucial to warehouse operations, ensuring that goods are organized, transported, and stored efficiently. However, manual palletizing poses significant health risks to workers. According to the Occupational Safety and Health Administration (OSHA), improper lifting and repetitive motion injuries are among the most common workplace hazards in the manufacturing and logistics industries. Investing in ergonomic palletizing equipment can help mitigate these risks by reducing the physical strain on workers and minimizing the likelihood of injuries.
Key Benefits:
1. Reduced Workplace Injuries
One of the most compelling reasons to adopt ergonomic palletizing equipment is the significant reduction in workplace injuries. Devices such as lift-assist systems, vacuum lifters, and automated palletizers help minimize workers' need to manually lift heavy loads. The reduction in physical strain leads to fewer injuries and decreased absenteeism, saving companies substantial costs in workers’ compensation and lost productivity. The National Institute for Occupational Safety and Health (NIOSH) has highlighted the benefits of ergonomic interventions in reducing musculoskeletal disorders (MSD) and improving workplace safety.
2. Increased Efficiency and Productivity
Ergonomic palletizing solutions streamline the material handling process, allowing workers to complete tasks faster and more accurately. Automated palletizing systems can handle high volumes of products with minimal human intervention, reducing cycle times and increasing throughput. This efficiency boost enables businesses to meet customer demands while maintaining high standards of quality and accuracy. The Material Handling Industry (MHI) reports that companies utilizing automated material handling solutions experience significant improvements in operational efficiency.
3. Enhanced Employee Morale and Retention
A workplace that prioritizes ergonomic solutions demonstrates a commitment to employee health and safety. Workers who feel safe and supported are more likely to be engaged, motivated, and productive. Additionally, reducing the physical demands of palletizing tasks can help retain experienced employees and reduce turnover, leading to a more stable workforce.
4. Cost Savings
While the initial investment in ergonomic palletizing equipment may seem substantial, the long-term cost savings are considerable. Fewer workplace injuries translate to lower medical expenses, reduced insurance premiums, and fewer disruptions due to worker absenteeism.
Types of Ergonomic Palletizing Equipment
1. Automated Palletizing Systems
Automated palletizers are robotic or mechanical systems that stack products onto pallets with minimal human involvement. These systems handle various products, from boxes and bags to drums and containers. Robotic palletizers, in particular, offer flexibility and precision, ensuring that items are stacked securely and efficiently. According to the Robotic Industries Association (RIA), robotic palletizing systems can improve accuracy and reduce workplace injuries.
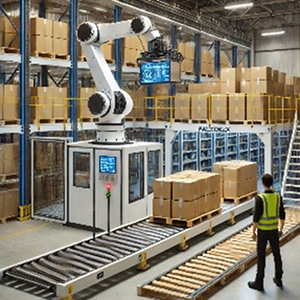
2. Vacuum Lifting Systems
Vacuum lifters use suction technology to lift and move heavy loads with minimal physical effort. These systems are particularly beneficial for handling awkward or bulky items, reducing worker strain, and improving overall efficiency.
.png)
3. Lift Tables and Pallet Positioners
Lift tables and pallet positioners adjust the pallet's height to reduce workers' need to bend or overreach while stacking or unstacking goods. These devices can be manually or hydraulically operated and help create an optimal working height, reducing fatigue and improving safety.
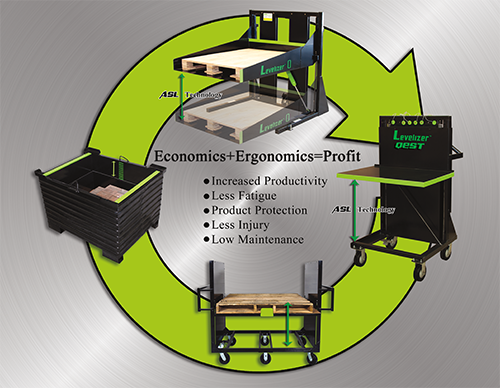
4. Conveyor Systems
Conveyor systems facilitate the movement of goods throughout a warehouse or distribution center, minimizing the need for manual lifting and carrying. When integrated with automated palletizing equipment, conveyors enhance workflow efficiency and reduce the risk of injuries associated with repetitive lifting.
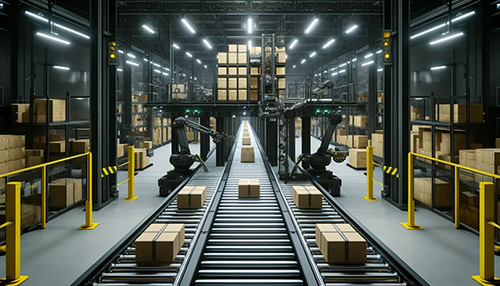
Key Considerations When Investing in Ergonomic Equipment:
1. Load Capacity: Ensure the equipment can handle the weight and size of your products.
2. Automation Level: Determine whether a fully automated or semi-automated system best suits your needs.
3. Space Requirements: Evaluate the available floor space and ensure the equipment fits seamlessly into existing workflows.
4. Employee Training: Provide proper training to workers to maximize the benefits of ergonomic solutions.
Conclusion
Ergonomic palletizing equipment is a game-changer for warehouses, manufacturing plants, and distribution centers looking to enhance efficiency, reduce injuries, and improve overall operational performance. By investing in automated palletizers, vacuum lifters, lift tables, and conveyor systems, businesses can create a safer, more productive work environment while reaping significant cost savings in the long run.
As workplace safety regulations continue to evolve, companies prioritizing ergonomic solutions will not only comply with industry standards but also gain a competitive edge in attracting and retaining skilled workers.
Sources:
Occupational Safety and Health Administration (OSHA): www.osha.gov
National Institute for Occupational Safety and Health (NIOSH): www.cdc.gov/niosh
Material Handling Industry (MHI): www.mhi.org
Robotic Industries Association (RIA): www.robotics.org
Diverse Manufacturing Solutions: www.DMS-Site.com
Nate Fugitt is a graduate of The Ohio State University and has been in the health and fitness industry for over three decades. Recently, Nate took the position of Business Development Director at Diverse Manufacturing Solutions (DMS) in Delaware, Ohio. His commitment to safety has been a lifelong career and a passion that has driven him to educate the public and develop innovative ideas to tackle the ever-changing landscape of worker safety. To learn more about DMS and their Levelizer® Ergonomic Palletizing Equipment, contact Nate at fugittn@dms-site.com.
|