Improper tool usage is one of the leading causes of injuries in the workplace, and it’s also one of the easiest to avoid. What bad habits can lead to these injuries? Complacency is a big one. Everyone knows they should adhere to practice proper tool use, but at times people may let their guard down, or take a shortcut. These lapses in judgement are some of the root causes that can lead to injuries.
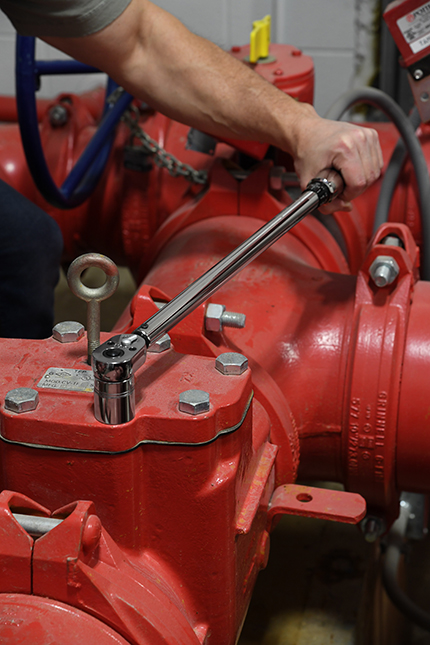
Establishing a safe working environment starts at the top. When facility leadership fosters a culture of safety, it empowers everyone to follow suit; the risk of accidents diminishes. While each facility will have its own needs regarding safety policies, these five tips are universally applicable to help you reduce workplace injuries from tools.
Use tools properly
Technicians should never modify a tool as it impacts safety and structural integrity. This tip may seem self-explanatory, but it serves as a good reminder. While manipulating or misusing tools can be tempting to a worker looking for a shortcut, using tools in unconventional ways or in a manner that they are not specifically designed for can increase the risk of injury, not to mention damaging the tool. Training sessions from a reputable manufacturer can help technicians understand how to use tools properly, and an open line of communication between staff and facility purchasing managers ensure that the proper equipment will be available for every need. Remember, if you modify or alter a tool, then you have the wrong tool for the job.
Inspect, clean and maintain tools regularly
Having the correct tools and using them properly is only the first step in preventing injury. All tools should be inspected regularly for any signs of wear that could affect the tool’s performance and make it unsafe. Dirt, grime and chemical solutions can erode material integrity and cause the tool to be inaccurate and need replacement sooner. In addition, undetected mechanical problems within the tool itself, such as chipping or a dull blade, can lead to further damage and technician injury. Implementing a tool inspection system that regularly checks for and resolves these issues is a fantastic defense against premature replacement needs and potential injury from a busted or dirty tool.
Maintain the surrounding area
Hazards can pop up anywhere in an active work site, and a technician focused on properly using a tool during a job may not notice potential issues in the surrounding area before they are injured. Keeping the entire space in proper working condition is a crucial and multi-faceted task. By assessing your area and enacting safety policies that keep floors clear and dry, access points reachable with a stable surface for the technician, clearly marked work zones and instituting other necessary safeguards, you can create the best possible environment for all workers in your facility. Even with these policies securely in place, accidents, spills or other unexpected events can cause problems. Consistent monitoring for potentially developing unsafe conditions, in addition to the policies in place to prevent them, will allow you to immediately detect and eliminate any obstacles to a safe workspace.
Use extra precaution when working at height
In examining ways to make drop prevention systems better for technicians working at height, industry has studied the most common cause of tool drops – the transfer between storage and use. More than half of drop incidents occur during this frequent action. With most systems, to secure a tool, the technician must first retrieve it and then clip or attach it to a lanyard. This process involves both hands and creates potential for dropped tools. This practice is one that required attention. When working at height, technicians should maintain three points of contact for their safety: two feet on a platform and one hand on a secured infrastructure. By using both hands to handle tools and attach the tool to a tethering device, the technician loses one point of contact.
To address this concern, tethering systems have been developed that eliminate the additional actions normally required to secure tools. An example is a tool belt in which each tool has its own pouch or holster with a tethering device already installed. This enables the technician to simply remove the tool, use it, and put it back into its place on the belt – all with one hand. Belts and harnesses can be custom designed to meet specific applications within different industries. Whether power generation, oil and gas, or utilities, systems can be designed with the proper tools, and ordered as turn-key solutions with a single part number. Every tool is already installed with its own tethered device and ready to be used: just open the box, put on the belt, and go to work.
Equip everyone with proper PPE
No matter what policies and precautions you put into place, it’s still difficult to prevent every possible accident. However, using the proper personal protective equipment (PPE) for the job can keep a small slip up with a tool from turning into a serious injury. Review your surroundings and evaluate the PPE needed to keep technicians safe while performing the work. The goal is to minimize risk, and one way to effectively do that is by keeping ample supply of the necessary PPE in stock, while also mandating that technicians use it every day.
These tips serve as a general guide to improving tool safety, but any further policy is up to you to determine. Each business is unique, and consulting with both your employees and the tool manufacturer is a great way to become as knowledgeable as possible about the uses and potential risks of the tools used at your specific site and drive effective policymaking. Tool-related injuries are prevalent and can quickly become deadly, but you can help prevent them.
Avoiding workplace injuries from improper tool use starts with creating a safe work environment. The key is to educate and motivate staff of all skill levels about tools. By establishing a safety-first mindset, you form a culture that avoids complacency and embraces the right way to do things … and that starts at the top.
Bobby Leitz is the national sales manager for Williams. He can be reached at Bob.t.leitz@snapon.com; https://www.williams-industrial.com/us_en/ |